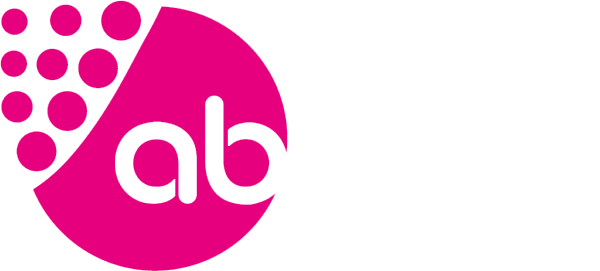
Watch our webinar on improving your environmental monitoring processes here. Originally broadcast on the 22nd of July 2021.
28th Jul, 2021Dr Tim Sandle discussed a risk-based approach to environmental monitoring with a focus on sample selection & trending of data.
Enric Adserà followed to present a case study from B. Braun who have implemented the SherpaPharma environmental monitoring software across two of their sites.
Can you touch on the resources to conduct a cleanroom validation (EM)?
Tim: The resources include a cleanroom contract company, who have airflow velocity measurements, smoke generator for airflow visualisation, and a bolometer to assess cleanroom air change rates.
For particle assessments, an air particle counter is required. For environmental monitoring, an active sampler is needed.
In terms of human resources, this depends on the size of your facility. Perhaps one contractor and one microbiologist per four rooms?
What kind of cleanroom clothing is recommended to avoid contamination?
Tim: For Grade C and D the clothing can be non-sterile, for Grade B the clothing must be sterile. Either re-laundered suits or disposable suits can be used. This comes down to cost and operator comfort. Disposable suits tend to be made from Tyvex and irradiated; re-laundered suits are a form of polyester. It is important to assess how often they can be laundered and still keep their filtration properties (industry standard is 25 to 50 times).
How often should you assess your RAs?
Tim: I would recommend every two years, or more often if signalled by a change control or other event that causes an impactful alteration to a facility or working pattern.
How often would you review your routine monitoring locations i.e perform additional monitoring to identify new locations to monitor?
Tim: I would recommend every two years, or more often if signalled by a change control or other event that causes an alteration to the cleanroom. In terms of additional monitoring, it can be a good idea to start with more locations and then reduce based on the data – perhaps after three-months or 50 samples?
Are there any guidelines specific to EM sampling locations ?
Tim: Not really, although hopefully the webinar helped.
Annex 1 recommends a risk based approach. I would include: where people are, where product is exposed, along transit routes for people or equipment, and to assess shard to disinfect locations.
How to select environmental monitoring plates location in newly developed area mainly sterile manufacturing area. What is frequency about identity microorganism found in house monitoring?
Tim: In sterile manufacturing I would use airflow studies and target depyrogenation tunnel outfeed, point of fill, and stoppering areas as a minimum,
For organism identification, all Grade A and B. For Grade C and D, I would target 25% to gain an overview of the indicative microbiota.
My company are looking to adapt their LIMS system for managing EM data. Is that easier that having another piece of software?
Tim: In my experience IMS does not work well with EM, especially where additional samples are required or with trending. This is why specialist systems are useful, like Sherpa.
Enric: Clearly not. Adapting a LIMS system to fit the Environmental Monitoring process is very complex, expensive and long. And the final result is not a good result. There are 3 main reasons:
SherpaPharma has been developed specifically to fit the demands of this variable process and with very powerful microbiological tools.
Which material is used as a sticker for the monitoring locations using Sherpa?
Enric: Support is made with Plastic material that can be used in clean room. The ink is special, resistant to any type of chemical used in clean room (alcohol, isopropanol, peroxide, …).
For more information on SherpaPharma visit our dedicated page here.
Or SherpaPharma’s own website here.
For a personal demonstration please contact us here.